Laser processing has emerged as a novel solution in marine maintenance. Handheld laser cleaning tools are now widely used in shipyards, drydocks and aboard ships to remove rust, old paint, biofouling, and chloride salts. Compared to other surface treatment methods, laser cleaning offers significant advantages, particularly in terms of worker safety and environmental preservation. Adopting this technology helps prevent the release of toxic chemicals and harmful particles into local aquatic ecosystems, minimizes waste, and conserves resources.
CleanTech & Marlin by Laser Photonics
Handheld laser cleaning tools such as CleanTech and Marlin by Laser Photonics rely on laser ablation to remove unwanted particles from metal and nonmetal surfaces. Every material has a certain ablation threshold; when this threshold is surpassed by an intense laser beam, the material’s particles are vaporized, leaving little to no dust. The underlying material remains unaffected due to its different ablation threshold. This thermal process is contactless, requiring no physical force from the operator and exerting no mechanical pressure on the workpiece.
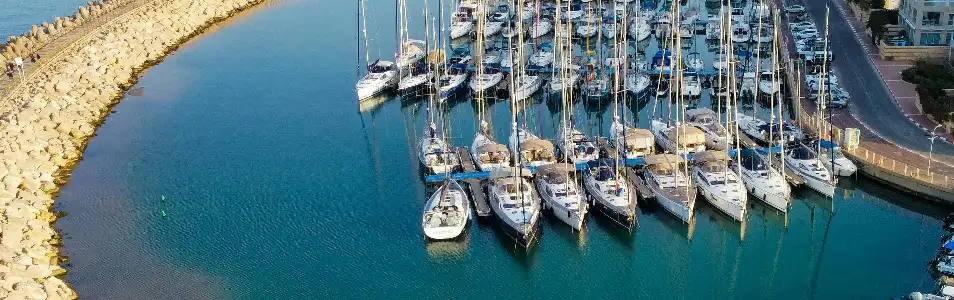
One Solution, Many Applications
Laser cleaning systems are highly versatile, effective on various contaminants and top layers including oxidation, scale, anti-rust coatings, paint, soot, oil, wax, epoxy, anodization, and other substances found in shipyard environments.
Rust & Scale
Spotting and removing corrosion early can save your cruiser from extensive, costly repairs. Once rust sets in, it tends to spread and cause further oxidation, especially in the presence of moisture and salts. If left untreated, it can weaken metal to the point of pitting, shortening the lifespan of boat components. If you see signs of corrosion, look for its source – it may be welded joints with anodized aluminum, bolts or fasteners with mixed materials, crevices or any metal area with damaged coating.
Paint Layers
Over time, layers of old paint on a boat’s hull can build up, warp, and create drag. In preparation for a new coat of paint, common practice is to remove existing layers to ensure better adhesion and to inspect the surface for damage. However, typical paint removal methods like abrasive blasting and chemical stripping are often unsafe for local ecosystems.
Biofouling Control
Organic growth on vessel hulls raises two major concerns. The first is drag increase – the accumulation of microorganisms and algae increases surface roughness, leading to higher frictional resistance. This results in reduced fuel performance and diminished maneuverability.
The second biofouling issue is the transfer of invasive aquatic species. There are guidelines for biofouling management that discourage the release of waste dislodged from the hulls into the water to avoid the spread of invasive species. Methods like underwater jet blast cleaning do not work as an effective solution in this situation.
Chloride Salts
Chloride salts on vessels and infrastructure in marine environments can lead to material degradation. Salts deposited on metal and concrete penetrate the material over time, weakening it. This produces cracks in exterior finishes, leading in turn to corrosion and compromised aesthetics, and reduces the service life of structures.
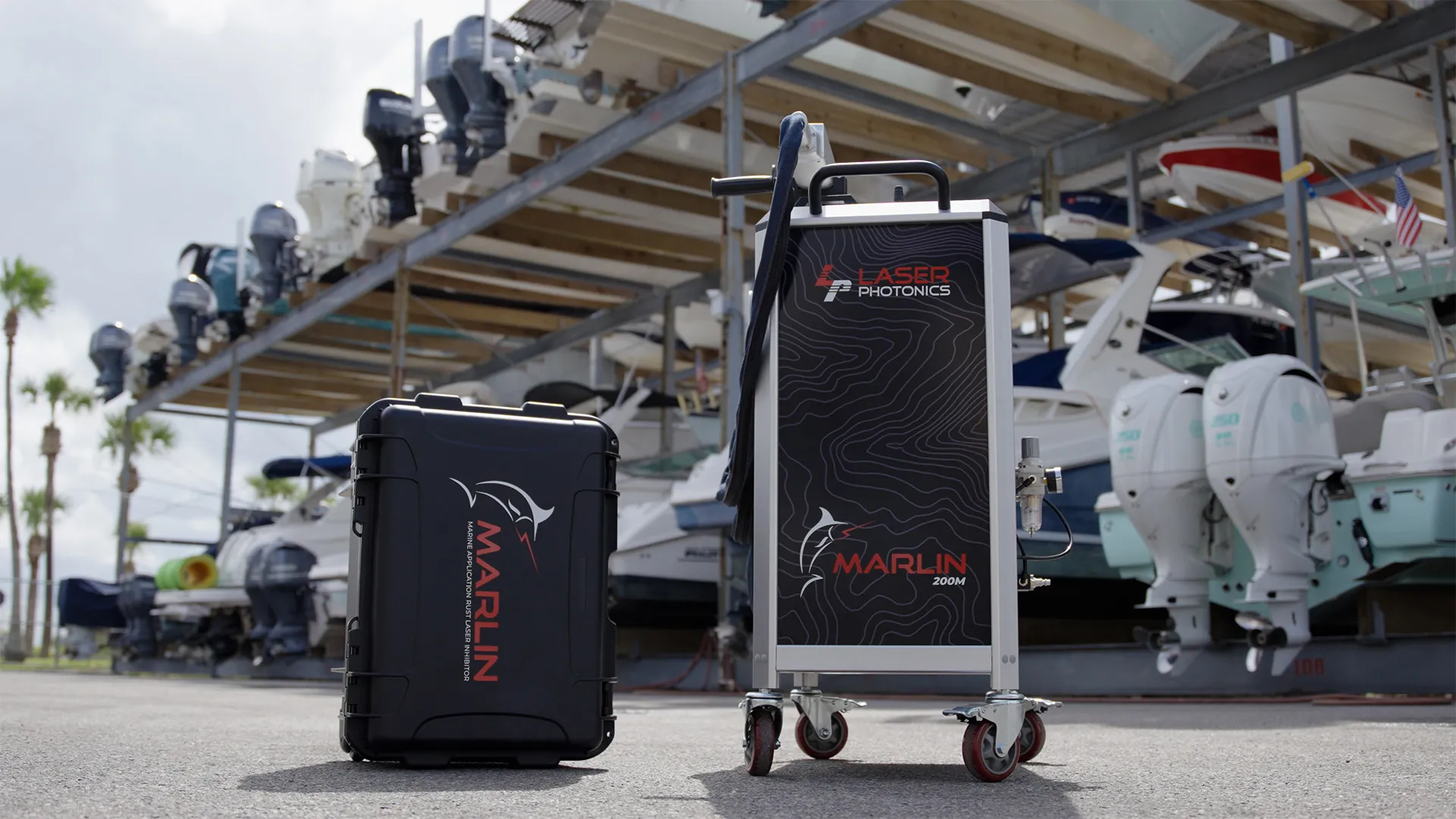
Hassle-Free Laser Cleaning
Laser cleaning is an ideal solution for mariners and shipyard professionals moving to minimize the environmental impact of their operations. Laser cleaning does not rely on hazardous chemicals or abrasive media to remove contaminants. This innovative method relies solely on electricity, with high-power laser units additionally requiring water chiller filling. During the procedure, little waste is produced, eliminating the need for time-consuming cleanup, waste disposal, and recycling measures. With proper use and maintenance, a laser cleaning machine by Laser Photonics will serve you reliably for years ahead, delivering a high ROI.
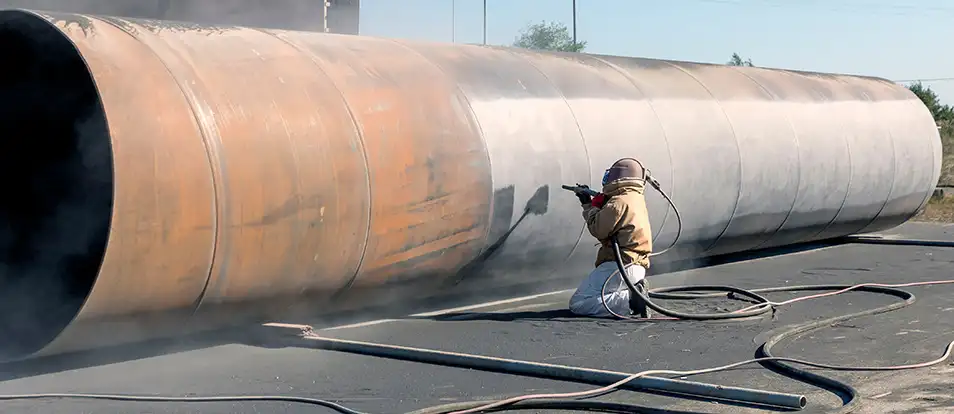
Partner With Laser Photonics
We are a publicly-traded (LASE) laser processing systems company trusted by small businesses, renowned global brands, and government agencies to deliver advanced laser machines for their unique applications. We are guided by the principle of sustainability in material processing, striving to create safer and cleaner workplaces while protecting the local environment. We welcome you to bring samples and visit our Customer Experience Center in Maitland, Florida, to see laser cleaning and other laser material processing equipment firsthand. Find out if it’s right for you!
Stay in touch with us on: