Laser component marking provides a reliable solution to facilitate traceability – a crucial process in modern manufacturing.
It’s a Friday afternoon. You are the production manager at a tire factory, and you get a call from a higher-up regarding an immediate recall of tire model T00 due to a flaw in the rubber layers.
The adrenaline rush comes over you as you grab your recall plan book. You know what to do! Immediately, you halt production at the rubber layering stage and notify the other areas in the plant that have been assembling the T00. The tires are removed from the line and shipping areas for quarantine pending the investigation. The shippers and warehouses are contacted and instructed to isolate these tires before they reach retail.
Luckily, this turns out to be a mock recall simulation, like a fire drill for manufacturers, to test the plant’s personnel and processes. Your company will analyze data from this mock recall to uncover potential vulnerabilities in its processes and fix them before a real potential crisis occurs.
After all, crises are bound to happen, but it’s how the business handles a situation that characterizes it and impacts its reputation.
If this was an actual recall, many questions would need answering. Was the fault due to the rubber or additives the company uses? Who supplied the raw materials and chemicals? Is the mixing and curing equipment working correctly? Was the manufacturer able to immediately trace the faulty tires’ location and journey?
Proper traceability would answer these questions and help rapidly localize the problem.
The Mechanics of Traceability
A mock recall is serious business, but an actual recall can be much more serious, especially when product defects can impact consumer safety and lives.
Take the 2000 Firestone and Ford tire recall, which involved the recall of at least 6.5 million tires. The tire defects caused tread separation and blowouts, which in turn resulted in Ford SUV rollovers and were linked to numerous fatalities. This incident not only highlighted the importance of product traceability but also led to the enactment of the Tread Act, a significant move in U.S. traceability regulations.
Effective crisis management during a product recall relies heavily on vigorous traceability systems and clear product marking. Utilizing effective marking tools during manufacturing ensures accurate traceability, prevents data gaps, enables swift withdrawal of affected goods, and ultimately restores consumer trust. Throughout the product’s journey, traceability helps ensure quality, safety, and regulatory compliance.
In manufacturing, traceability is not just about locating a product; it is the whole story, including the manufacturer, inspection details, production notes, date and time, batch number, and where the raw materials were sourced from. It is documenting products through all assembly and distribution points.
And it’s the tracking information on every product that helps the manufacturer to keep itself and its suppliers in check and utilize the data to fully control processes, optimize operations, and maintain product quality.
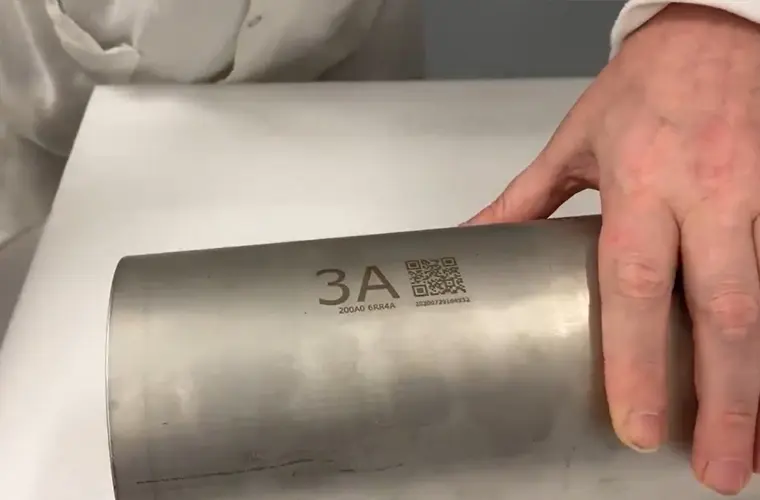
Batch numbers track groups of products, while serial numbers track individual items. They enable companies to identify failures, execute targeted recalls, and minimize the scope of product withdrawals.
To track a product through the supply chain, you need unique identifying marks on parts. Upstream tracing follows the product’s journey backward to its origin, useful for recalls or regulatory issues. Downstream tracking monitors the product from manufacturing to its final destination, helping analyze the entire supply chain. Effective internal traceability allows you to assess production procedures and identify problems through root cause analysis.
In all, accurate traceability is about using all collected data to consistently improve your operations for better quality, efficiency, and cost savings.
Product Identification With Laser Marking
Traceability systems require each product and its components to be labeled for identification. These marks allow for the parts to be scanned as they pass through various stages of production.
One novel method of labeling components is utilizing laser marking technology. Laser marking systems are highly effective at producing precise, permanent, traceable codes and are easily integrated into production lines. Unlike sticker labels or ink, laser markings remain clear and do not wear off over time.
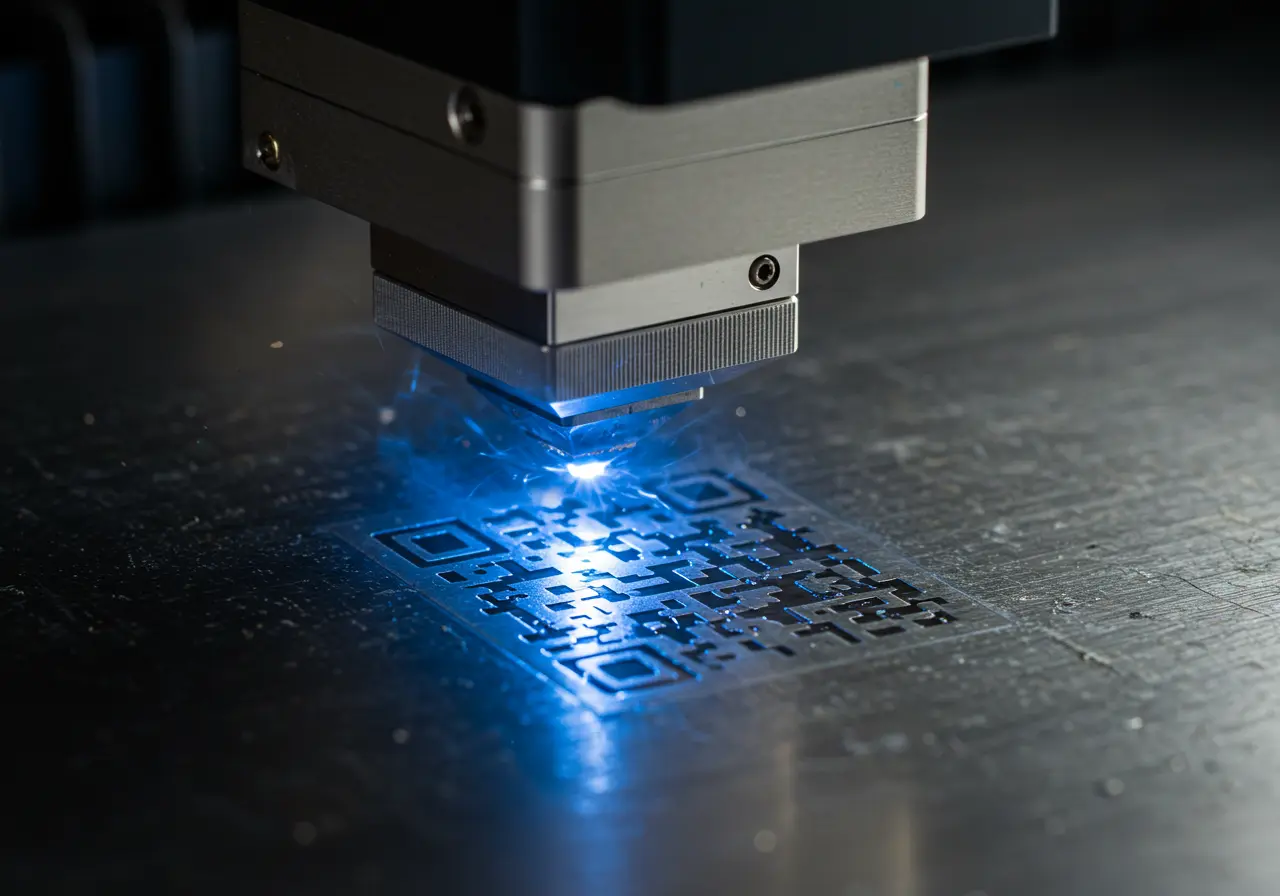
With the critical need for reliable traceability systems, especially in heavily regulated sectors like food, medical, automotive, aviation, and defense, laser marking technology presents a powerful solution. It is an ideal tool for meeting strict traceability requirements in adherence with manufacturing regulations, preventing counterfeit retail, supporting quality control and inventory management, and improving overall production efficiency.
Laser Solutions by Laser Photonics
Answering the need for permanent product marking brings us to the innovative marking solutions offered by Laser Photonics, a company at the forefront of laser technology. We provide laser marking equipment that ranges from compact, handheld options under the MarkStar line to LaserTower stationary systems designed for easy integration into production lines. All systems are low-maintenance and require no consumables.
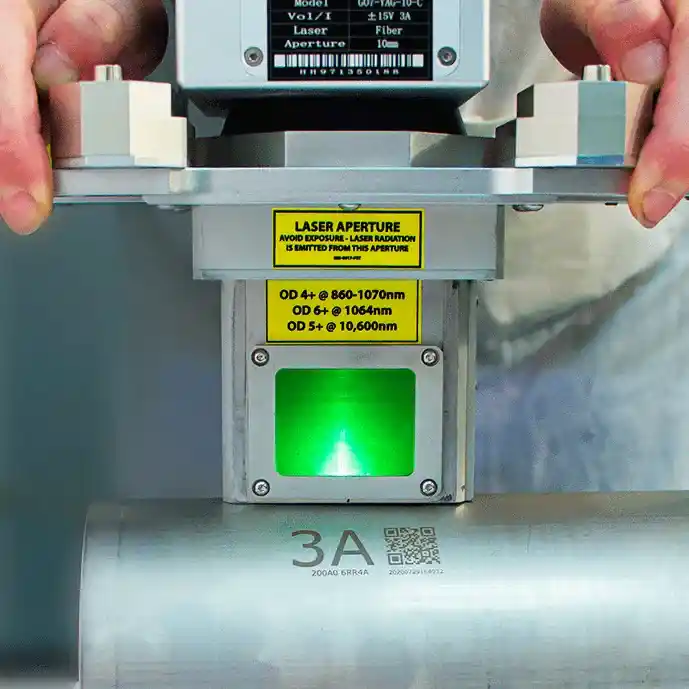
To highlight one of our MarkStar systems, consider the MSIM-1020. This handheld fiber laser marker offers portability without compromising precision, making it ideal for on-the-go marking. The MSIM-1020 produces marks on a wide range of surfaces to keep your traceability systems running smoothly and efficiently. Its marking area is 4 x 4 inches; other configurations are available.
This stationary engraving system under the LaserTower product line – the LTIE-3050 – is an ideal solution for semi-automated high-volume laser marking in production lines. It’s a CDRH Class I system with a fully enclosed design that confines the laser radiation workspace.
All our laser marking systems enable modern product traceability solutions by producing permanent marks through laser ablation. Due to this durability, laser marking is becoming the top choice for manufacturers aiming to enhance their traceability capabilities.
From Crisis to Confidence
If our hypothetical mock recall took place in reality, a crisis could be minimized if the company had the proper traceability systems in place, all components were marked, supply chain information was up-to-date, and all personnel knew the procedure.
Traceability systems reflect a company’s commitment to product safety and quality, aligning with core values like integrity, trust, and accountability. By monitoring processes throughout the supply chain, traceability reinforces safety and quality standards, ultimately supporting customer satisfaction and preventing issues.
In today’s market, consumers are more interested than ever in knowing where their products come from and how they’re made. Traceability has become the number one way for brands to exercise transparency, ensuring their products are genuine, safe, and sustainably produced, increasing customer trust and loyalty.
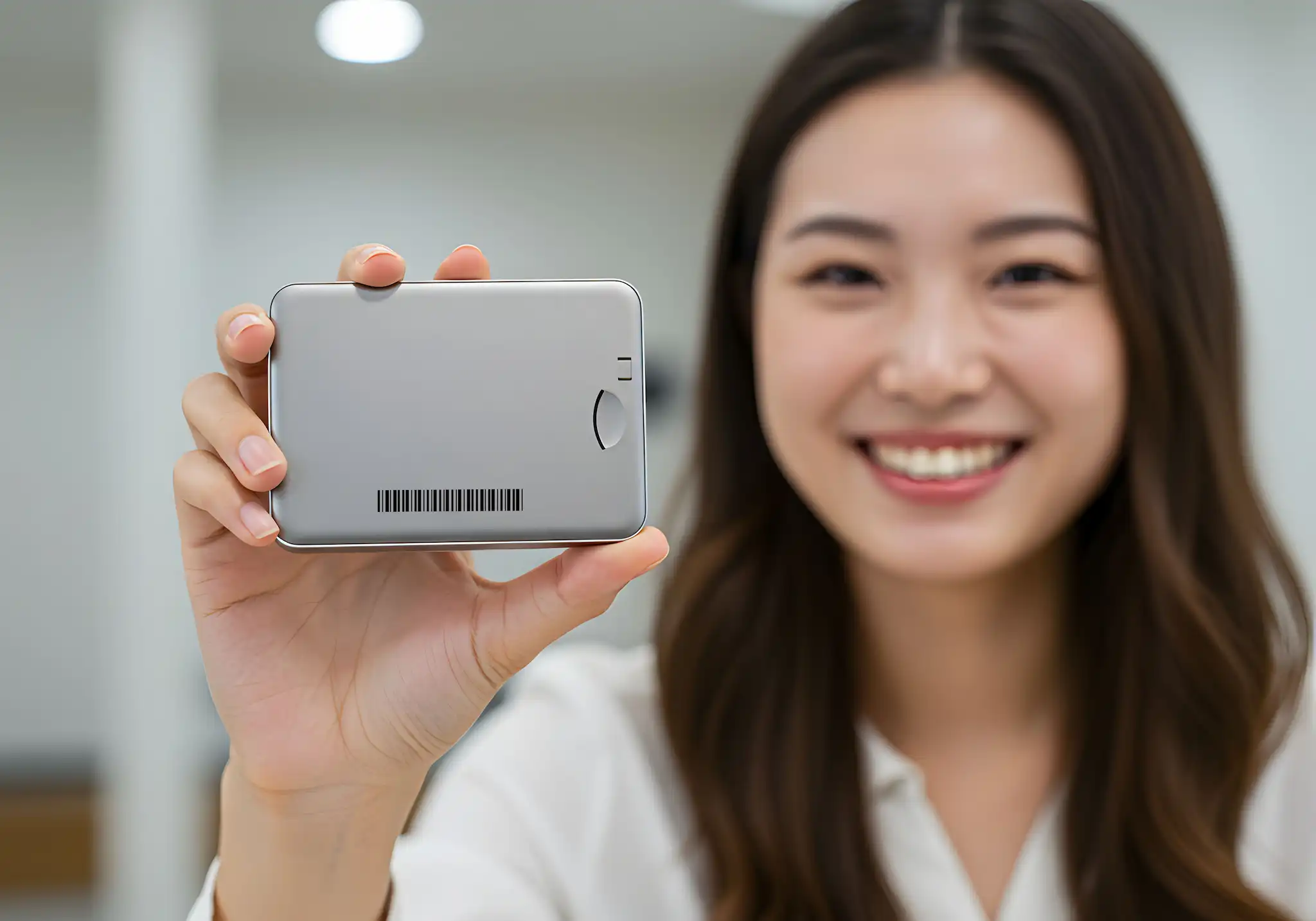
Traceability develops confidence at all levels of a company. By providing a clear and accessible history of every part and product, traceability empowers the workers who mark and scan parts with the knowledge that their contributions are critical to the overall quality and reliability of the final product. As to the upper management, this transparency enables them to make informed decisions based on accurate data, which is crucial during recalls or audits.
Ultimately, traceability creates a shared understanding and accountability, improving the confidence of everyone involved in the manufacturing process.
Enhanced through laser technology, product marking is necessary for strong traceability systems within modern manufacturing. Laser marking ensures the creation of durable, high-quality identifiers vital for meeting stringent traceability standards and optimizes processes where other approaches lack momentum.
Consider Laser Photonics as your trusted provider of laser marking technology. Our laser marking solutions cater to different operational needs, with custom configurations offered to best suit your product materials and production lines. From the compact MarkStar laser systems to the LaserTower stationary workhorses for high-volume production lines, our solutions will answer your needs for precision marking.
Speak to a laser specialist today!
Speak to a Laser Specialist
Stay in touch with us on: