Abrasive blasting is positioned as one of the most effective methods of surface preparation, and it has been so, particularly in high-volume, heavy-duty applications. Yet this method has plenty of drawbacks on multiple levels – that may have swayed you to seek an alternative approach for your business.
One such alternative is laser cleaning technology. In this blog, we cover the top five reasons to transition to laser technology as your new cleaning method of choice.
The Gritty Nature of Abrasive Blasting
If you have tried it, you know. From inside the heavy and bulky protective equipment, with earmuffs over your ears and respiratory equipment over your face, you press the trigger and your arm jolts back as the pressurized stream of abrasive media hits the surface at a high speed. And it gets everywhere! So, you know that when you’re done (cleaning, smoothing, or etching), you have a lengthy, tedious cleanup to take care of.
And if you weren’t careful in your containment prep work, this hard-to-collect airborne dust – now a mix of abrasive media, the coating you removed from the workpiece, and possibly particles of the workpiece itself – settles on all surfaces, accumulates in crevices, and ultimately disperses in the environment. If your abrasive media of choice is walnut shells or dry ice, the environmental damage from your project may be minimal. But the particles of aluminum oxide, for example, which is advertised as “environmentally friendly compared to other abrasive materials,” can be harmful to living organisms in acute and chronic cases, as studies suggest. Not to mention sandblasting using sand with a high percentage of quartz – this is associated with serious respiratory issues in workers.
How a Laser Cleaning Machine Works
Laser cleaning is quite a different process. This technology uses the thermal impact of infrared light to evaporate contaminants or coatings off solid surfaces. This process relies on laser ablation – the energy from the laser pulse is absorbed until the ablation threshold is reached, upon which the material’s molecules break apart. Each material has its own ablation threshold; this makes the cleaning process very controllable and precise.
How To Work a Laser Cleaning Machine
Laser cleaning systems come in various configurations – from compact, handheld tools for fieldwork to automated, enclosed machines for high-volume throughput. To work a laser cleaning machine, hook it up to electric power and air pressure; high-power laser tools come with a water chiller and require water. Make sure to wear proper safety eyewear and shield the process from bystanders – and that’s it! Choose among the system’s preset lasing patterns or fine-tune its settings manually according to your material and the degree of contamination. Direct the scanhead at the workpiece, press the button, maintain focus, and observe – no physical force required.
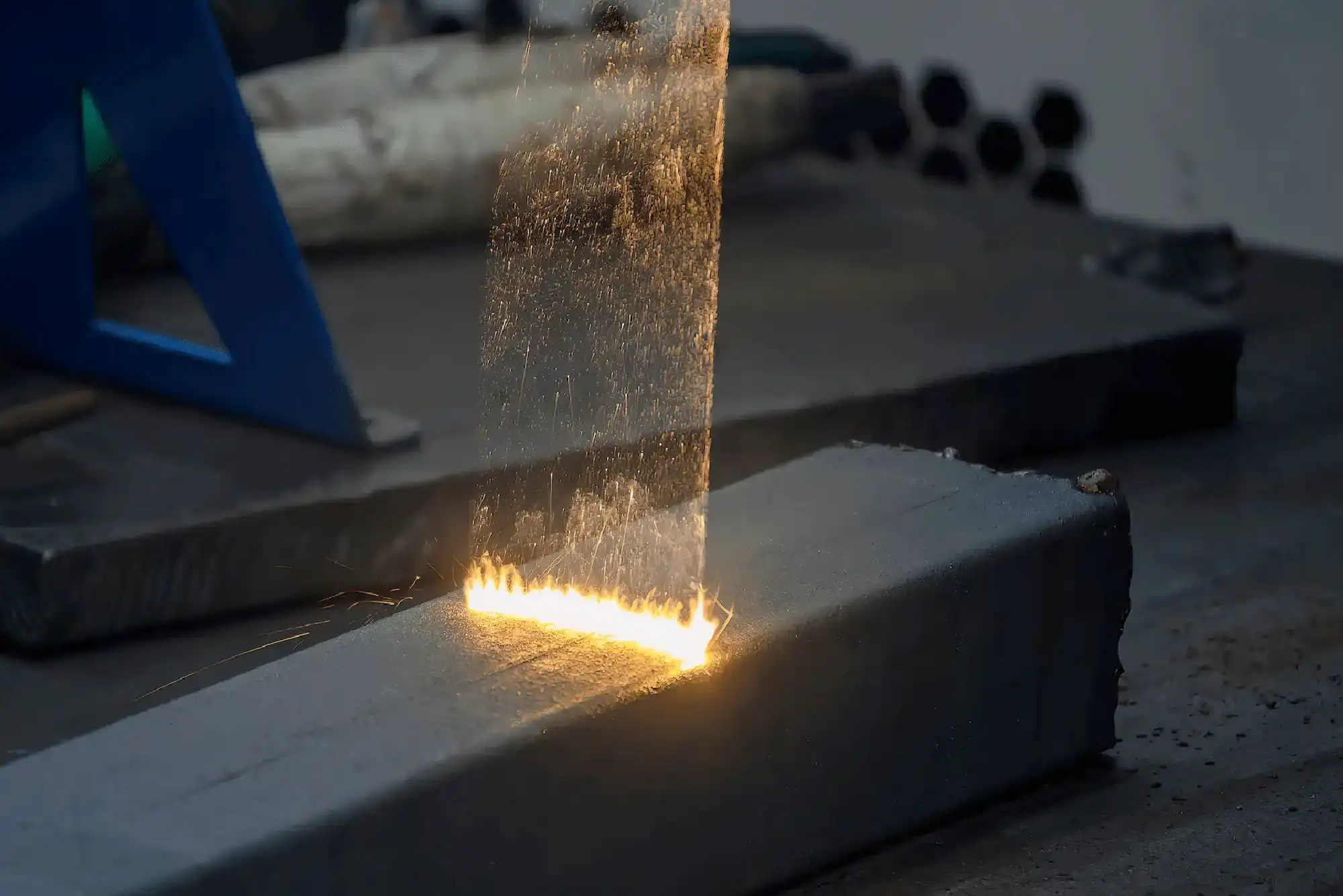
Top 5 Reasons To Adopt Laser Cleaning
1. Operator Safety
Safety eyewear must be appropriate for the specific laser’s full range of wavelengths and sport peripheral vision protection. A laser cleaning machine by Laser Photonics requires safety goggles with optical density (OD) of 5 or higher. Or opt for our enclosed, semi-automated Class I laser systems that are safe to operate without vision protection measures.
To start with the basics, ditch the bulky protective equipment. The one (but serious) safety measure in laser cleaning is protecting your eyes, as well as the eyes of anyone nearby. Infrared laser light, while invisible to the human eye, reflects off surfaces and may damage the retina, if accidentally exposed.
No ecosystems will be hurt in the process. No need for abrasive media, no hazardous chemicals, no single-use protective equipment, and nearly no waste. Laser cleaning vaporizes, rather than scratching off, unwanted material, which generates waste in minimal quantities – in the form of dust that is easy to collect. This greatly reduces the need for waste disposal and recycling measures.
Should your processes involve the ablation of toxic coatings, opt for laser cleaning configurations that integrate a vacuum nozzle, vacuum table, or fume extractor as additional containment measures.
The precision you get with laser cleaning is beyond compare. As said earlier, the materials’ varying ablation thresholds make laser processing highly controllable and allow for the selective removal of layers. This is particularly beneficial in high-detail applications like asset restoration, PCB manufacturing, chip fabrication, and medical device manufacturing.
Moreover, as a non-contact process, laser cleaning puts no impact stress on the base material. Specifically for the fine detailing of thin metals, Laser Photonics offers finishing-grade pulsed laser tools in various power configurations.
A hefty initial investment leads to hefty returns in the long term. A high-performance laser cleaner with U.S.-based training and support does come at a price. But with proper handling, laser tools require minimal upkeep and provide reliable, consistent performance for years. By equipping your team with laser cleaning technology, you minimize prep work, post-process cleanup, material losses, and use of consumables, saving in turn on labor, time, and costs.
A variable-settings laser cleaning tool can be remarkably multifunctional. Contaminants and coatings, including corrosion, soot, paint, powder coating, zinc plating, and even radioactive particles, are effectively removed via lasing off a wide range of materials. (Just imagine attempting nuclear decontamination with sandblasting – that would be a fiasco!)
Moreover, when its settings are adjusted, a laser cleaning machine by Laser Photonics turns into a conditioning tool that can yield a textured or polished surface. Opt for one of our high-power roughening systems if you are looking to improve the adhesive properties of your materials.
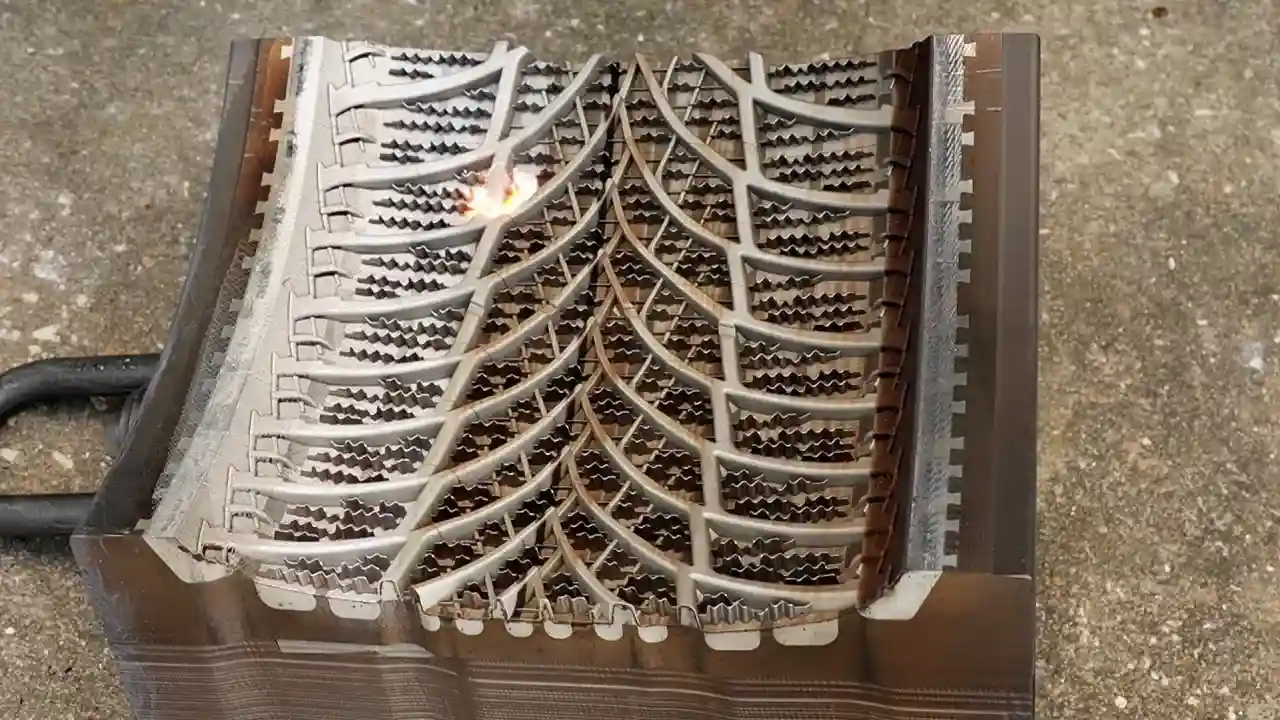
An Essential Tool for Daily Work
“At Taller de Soldadura Rodríguez, the innovative equipment from Laser Photonics has really simplified our work, facilitating layer-by-layer removal of rust, old paints, and dirt. The laser cleaner is efficient, and its functionality is exceptional. It has become an essential tool for the daily work at our welding workshop. Without a doubt, our clients are delighted with the result. Thank you, Laser Photonics, for your customer service and training.”
~ Jonathan Rodríguez Zúñiga at Taller de Soldadura Rodríguez
Join Our Community of Laser Tech Lovers
At the end of the day, the surface prep technology you use in your operations will always depend on what’s best for your task at hand. If our Top 5 Reasons convinced you that laser cleaning is the way to go, but you still have a few bags of abrasive media to spend, keep us in mind and come back to us when you’re ready. In the meantime, join our sustainability-minded community of laser tech lovers and follow us on social media.
Contact Laser Photonics with any questions you may have about laser processing to find out more. We specialize in laser-powered solutions for eco-friendly cleaning, “cold-cutting,” precision marking, and narrow-seam welding, and we offer custom engineering services.
Stay in touch with us on: