“Rust never sleeps,” sang Neil Young back in the 70s. The legend used the persistence of rust to draw a parallel with the nonstop societal decay. You might have heard how the Statue of Liberty herself came close to toppling down before its repair in the 80s – in part due to the corrosion of the structural connections in her interior. Today, the battle against physical rust persists without a once-and-for-all solution and incurs billions of dollars in financial impact.
Across the internet, photos of the Navy’s ships with visible rust streaks draw public attention. Whereas our fleet gets deployed all around the globe and stays offshore over extended periods, foreign naval ships staying close to their dry docks tend to appear newer and better maintained. And when our ships look like they are in ill repair, our capabilities appear questionable to our allies and enemies alike.
Indeed, the battle against rust cannot be won once and for all, but regular maintenance can help keep it under control. For the Navy, this means that maintenance must be continued offshore.
Now, the Navy has a new, modern tool in its arsenal in the battle to maintain its fleet. Laser cleaning technology from Laser Photonics can blast the rust off ships, even when they are at sea.
The Rust Offensive
Why is rust such an issue? It is basic science – a result of the combination of air, water, and iron or dissimilar metals. When iron (or an iron alloy) is exposed to oxygen and moisture, an electrochemical reaction occurs. Over time, the hydrogen and oxygen atoms bond with iron atoms, creating iron oxide, or rust – a form of corrosion. This “bonding” weakens the metal structure to the point of disintegration.
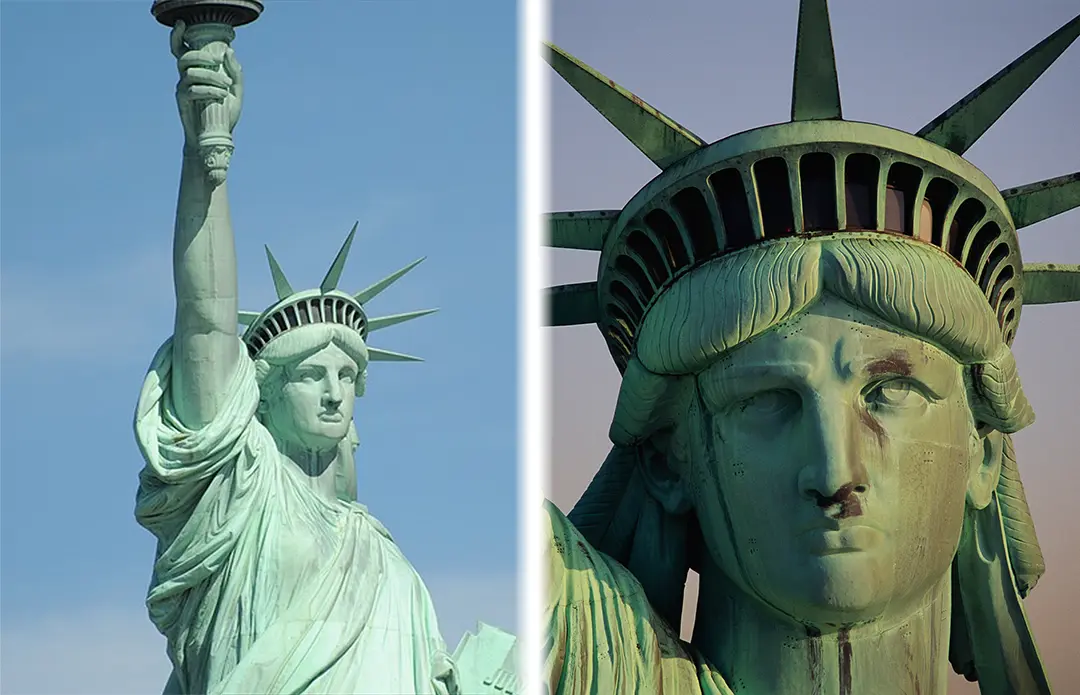
In the case of the corroding Statue of Liberty, engineers ended up replacing its iron armature with stainless steel and insulating its copper skin. This comprehensive, time-consuming approach is not an optimal scenario for most cases – the Naval fleet included. Ships corroding in the U.S. Navy cannot afford to wait until they are on the verge of failure to start maintenance – and replacements may not be an option in that environment.
Ships are usually constructed from mild steel because it offers an excellent balance of strength, durability, affordability, and ease of fabrication, making it a suitable material for large ship construction. The downside is that mild steel also has a high iron content that, if left uncoated or coated improperly, is very susceptible to rust.
The financial impact of corrosion on military assets has been immense – reported by the DOD at $20.6 billion in 2016. For just the Navy alone, which includes ships, submarines, and aircraft, the figure was at $8.6 billion. And this does not include the costs of mission delays, lost opportunities for hours and funds spent on maintenance, and shortened equipment lifecycles.
Defense Strategy
To combat rust, the Navy tasks sailors to perform regular maintenance, while the ships are also scheduled for repairs and re-painting at a dry dock every five to seven years. A combination of these efforts serves to keep corrosion at bay.
The prescribed method to remove rust is to first remove the rust deposits and then coat the surface with primer and rust-resistant paint. This often requires the current paint to be removed to expose the corrosion beneath. The Navy goes through roughly 25 to 30 million gallons of paint per year to maintain its fleet. That’s a lot of paint!
The Navy must play a balancing act with assigning crews to maintenance duties while keeping up its high operational tempo at which a ship is actively engaged in operations. When a ship needs to deploy rapidly, it can’t call a timeout to finish maintenance and clean up. This makes the scheduled repairs harder to keep up with. This situation creates a backlog of maintenance, while rust stains accumulate.
During extended time at sea, several factors get in the way of ship maintenance: weather conditions, proper training, and the shortage of sailors to perform the tasks.
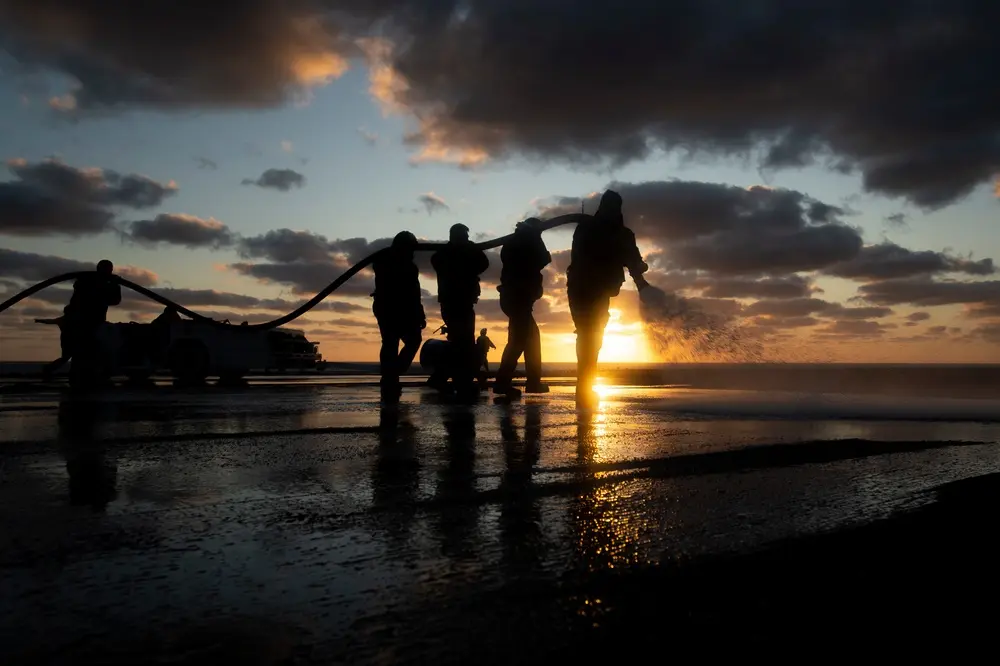
According to a Government Accountability Office (GAO) report from late 2024, 63% of executive officers surveyed stated that the shortage of sailors made it difficult to complete required repairs while at sea.
The report also found that sailors felt that the number of crew members available was inadequate to meet the workload. Additionally, the sailors felt that the maintenance training they were given was insufficient.
An earlier GAO report found that instructor-led hands-on training had dropped off to the point where sailors had to learn through on-the-job training. Because of this, a ship’s upkeep was often given a low priority.
And the Navy’s recent budget further restricted the number of sailors; now, officers must do with less manpower to keep older vessels shipshape.
Arms for the Battle of Rust
While a vessel is underway, cleaning methods such as sandblasting are impractical anywhere onboard. The setup and breakdown are lengthy, abrasives are required, as well as numerous pieces of safety equipment. Hazardous waste must be contained before it can run off into the ocean, and the risk of exposure to contaminated media by nearby personnel and equipment is high.
Hand tools are common for smaller repairs – sandpaper, wire brushes, chipping hammers, and hand scrapers. Portable power tools, such as grinders and wire wheels, speed up the process and do a better job of removing substantial deposits. For intensive tasks, a needle gun is often employed. It uses a set of small, dull rods that reciprocate rapidly to chip away at old paint and rust.
The use of hand tools and power tools can get quite labor-intensive and time-consuming. These often come with excessive noise, generate dust and debris, and require physical force. Operators must wear protective gear and be resilient to vibrations. In addition, these tools may not be used on delicate surfaces due to mechanical stress.
Portable laser cleaning machines solve some of these issues. Let’s find out how.
Lasers to the Rescue
CleanTech laser systems by Laser Photonics can be used all over the ship, both on topside and below deck. You can also explore the DefenseTech line of laser cleaning systems, engineered specifically for military and naval applications. These are delivered by our sibling company, Fonon Technologies – a trusted provider of defense-grade, trade-compliant laser solutions for optimized maintenance.
The DTMF-1020, housed in a weatherproof case, is designed for small-scale, meticulous cleaning in the maritime environment, while the DTMR-3040 tackles heavy-duty, intensive tasks.
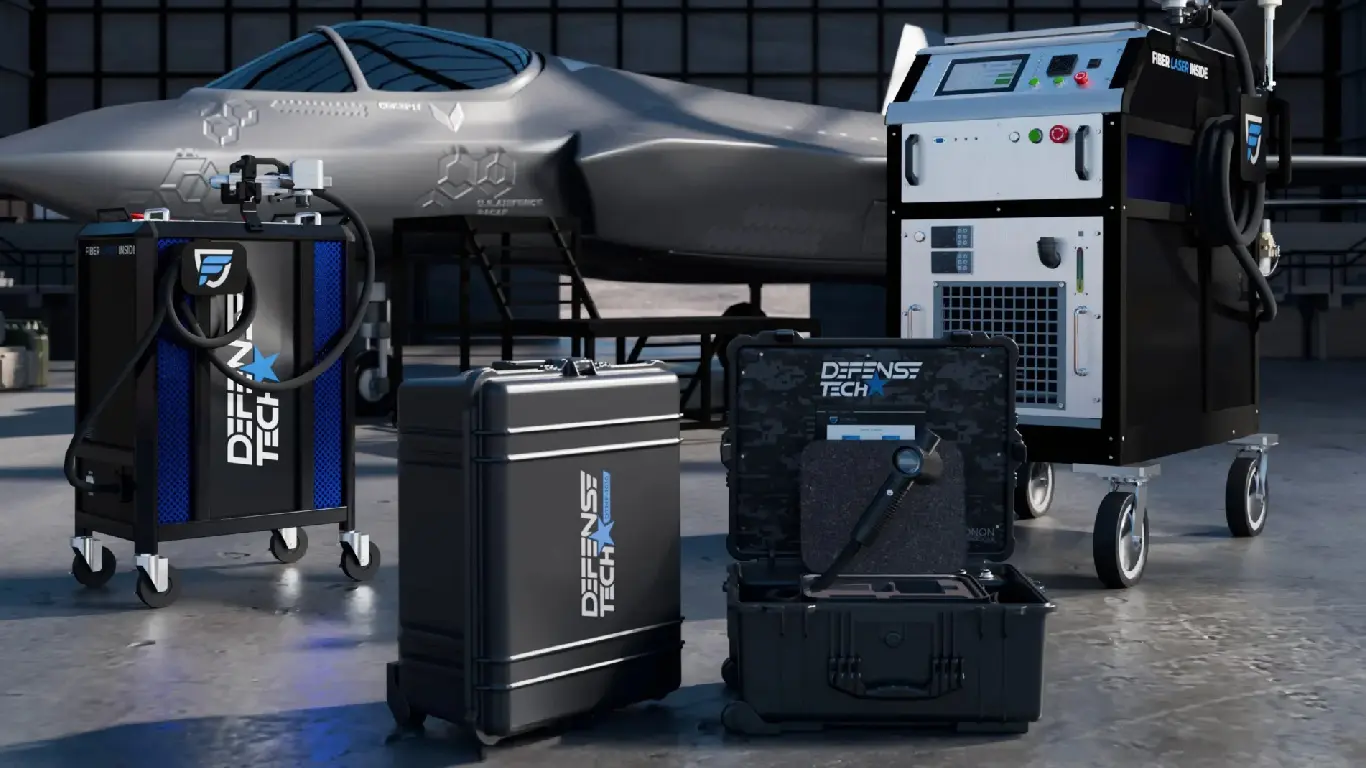
Our mobile laser cleaning systems are perfect for use on a ship and provide speedy, accurate, and targeted cleaning. A laser system integrates a handheld blaster connected by a cable to the main unit. Once the operator inputs the desired settings for the job, cleaning can be performed at a distance from the main unit and easily handled in hard-to-reach spaces.
Powered by a high-energy laser, the system removes contaminants much quicker than conventional cleaning techniques. This especially comes in handy when working below deck in tight, hot spaces where the bulkhead is heated by the sun on the steel hull. Laser cleaning allows sailors to complete the task in less time than traditional methods and quickly get out of that environment. When the repair is carried out in a small, enclosed space, a fume extraction system must be added to trap fumes and hazardous particles.
The versatility of laser cleaning offers the ability to remove a variety of other contaminants and coatings, not limited to paint, oil, soot, grease, and mold. A laser system can also be used for pre- and post-weld treatments when repairs are done onboard.
Laser technology reduces the use of chemicals and abrasive media in cleaning processes. No consumables are needed for laser cleaning, and there is no need for heavy, complex Personal Protective Equipment (PPE). Basic PPE for laser cleaning includes laser-rated goggles, gloves, and – when vaporizing toxic particles – a respirator.
As a non-contact method, laser cleaning induces no mechanical stress during processing and requires no physical force beyond handling the blaster. This eliminates repetitive use injuries that mechanical cleaning methods are associated with.
Laser Photonics provides training to crews using laser technology. These mobile machines are easy to set up, easy to master, and quick to stow away during rapid operational shake-up, no extensive cleanup necessary. A small preservation team can handle the entire procedure. Once rust is removed, coating or painting can be applied immediately, without additional steps in-between.
Parting Thoughts
Rust never sleeps, and it will always create problems when iron and air come together. Lack of proper maintenance not only affects the visual appearance of our Navy’s assets, but it can also lead to their deterioration and failure during operation. To fight rust effectively, the Navy must tackle corrosion at its earliest signs to prevent it from snowballing into a major issue interfering with operation readiness.
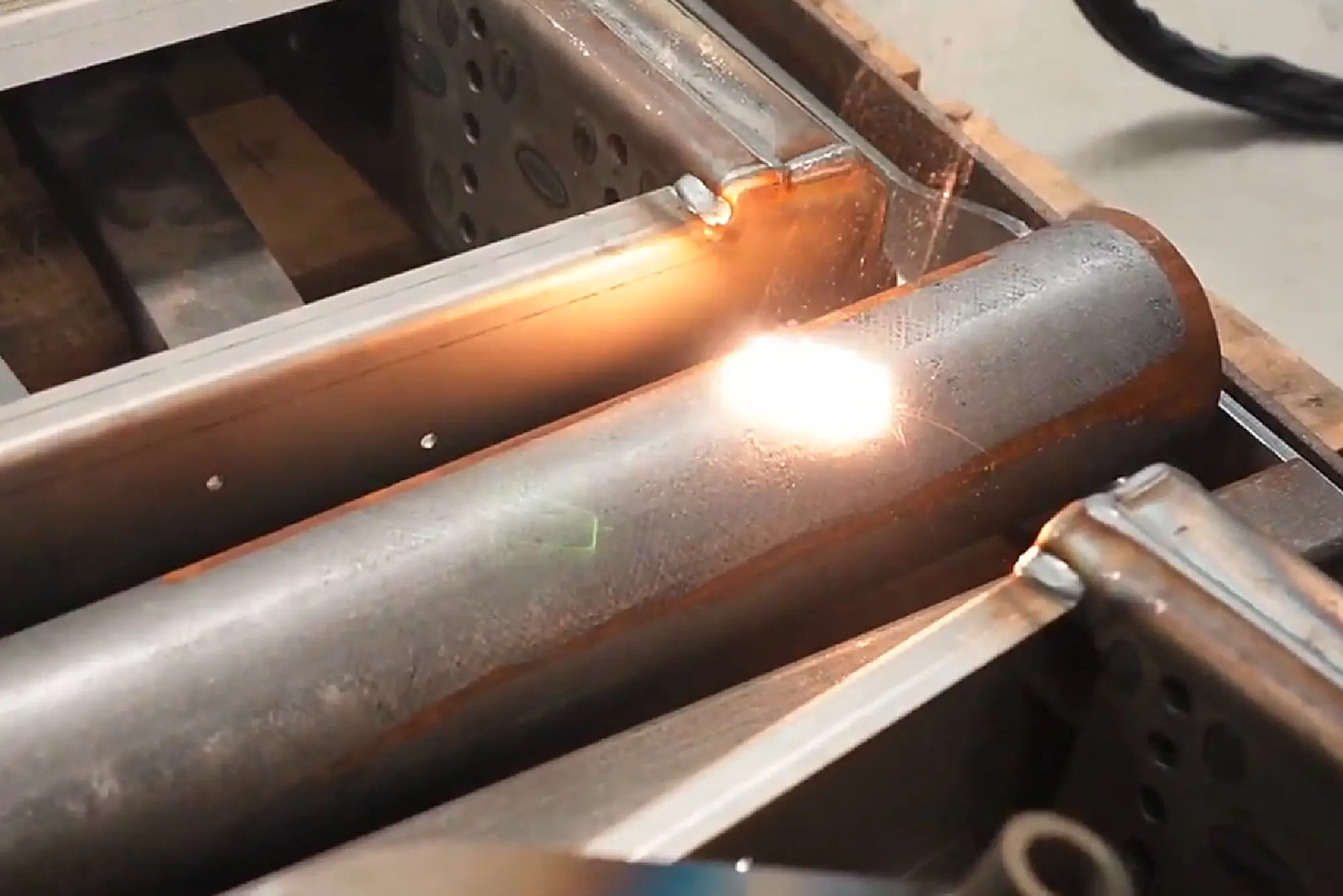
We have developed effective tools that keep rust on ships under control, both in the port and at sea. This technology is fast, cost-effective, safe for the environment and the operators when used properly, and it can help extend the lifespan of critical structures of a ship.
Adopting laser cleaning technology from Laser Photonics and Fonon Technologies greatly optimizes ship preservation, cutting back the maintenance funds and labor hours. A well-maintained and squared-away Navy ship not only embodies operational readiness but also serves as a symbol of the crew’s professionalism and the vessel’s preparedness for any mission.
Learn More About Our Laser Cleaning Systems.
Follow LaserPhotonics online for our latest updates : Facebook Instagram LinkedIn X