Sandblasting a Costly Practice for Sustainability-Focused Businesses
Removing a coating that is resistant or even bonded with a surface can be quite challenging, with just a handful of effective solutions available on the market that are usually coating-specific. Among such coatings and contaminants are epoxy, rubber residue, oil, paint, zinc plating, silicate deposits, and oxidation. Rather than applying a combination of degreasers, acids, and other case-specific chemical cleaning agents, companies commonly turn to sandblasting, an abrasive cleaning method that is considered inexpensive and suits a wide range of cases. However, sandblasting comes with a slew of issues in tow, and forward-looking companies have been on the lookout for a more sustainable solution for the workplace and environment.
Epoxy |
Rubber |
Soot |
Oil |
Paint |
Zinc plating |
Corrosion |
Silicate |
Anti-rust coating |
Electrolytes |
Powder coating |
Insulation |
Radioactive particles |
Enter Laser Cleaning
This innovative approach is making significant inroads in the industrial cleaning space, offering a cleaner and more environmentally friendly alternative to sandblasting. Rather than abrasion, laser ablation relies on thermal processing to vaporize unwanted layers into gas or alter the micro-surface for roughening and polishing purposes. Unlike sandblasting, laser cleaning requires no consumables and generates little to no waste. Plus, laser cleaning is not associated with health risks for machinery operators, requiring only eye and skin protection.
As we delve into the laser cleaning vs sandblasting comparison, it becomes clear that the latter not only offers a more sustainable solution but also redefines what it means to be cost-effective in the long run. This transition is not just about choosing modern technology; it’s about embracing a future where efficiency and safety are prioritized.
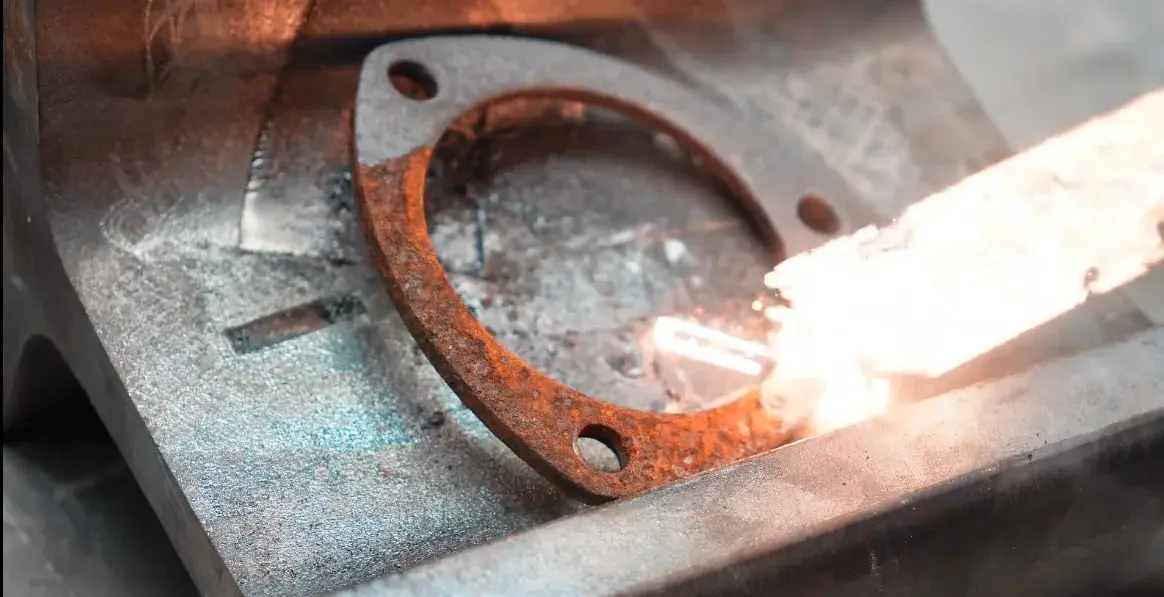
Affordability at a Price
Previously, blast cleaning involved propelling silica sand at high speeds onto the target. This abrasion would scrape off the unwanted coating and coarsen or smoothen a surface. However, inhaling silica dust has been linked to silicosis – a serious and irreversible respiratory disease. During sandblasting, silica sand breaks down into fine particles and becomes airborne; these particles can be inhaled by workers and settle in their lungs. Over time, these workers – exposed to silica dust in mining, glass and stone factories, and construction and repair environments – could develop difficulty breathing, tuberculosis, and lung cancer.
Between 1999 and 2014, silicosis was recorded as the main or contributing cause of 2163 deaths in the United States. This figure is said to be under-reported, as an estimated 2.3 million people in the country are exposed to respirable crystalline silica (RCS) at work.
Most developed countries have long had laws in place that ban the use of abrasives containing more than 1% free silica. In the United States, reducing the silica exposure limit was slower in enactment, despite longstanding recommendations by a division of the Centers for Disease Control (CDC), the National Institute of Occupational Safety and Health (NIOSH). The Occupational Safety and Health Administration (OSHA) proposed the modern silica law only in 2013 and got it codified in 2016, lowering the permissible exposure level to 50 micrograms per cubic meter of air (0.05 mg/m3) over an eight-hour shift. The action level was set at half that amount: at the 25-microgram threshold, action to mitigate risks must be taken.
That was a long-overdue revision of the 250-microgram figure set for the construction and maritime industries in 1971.
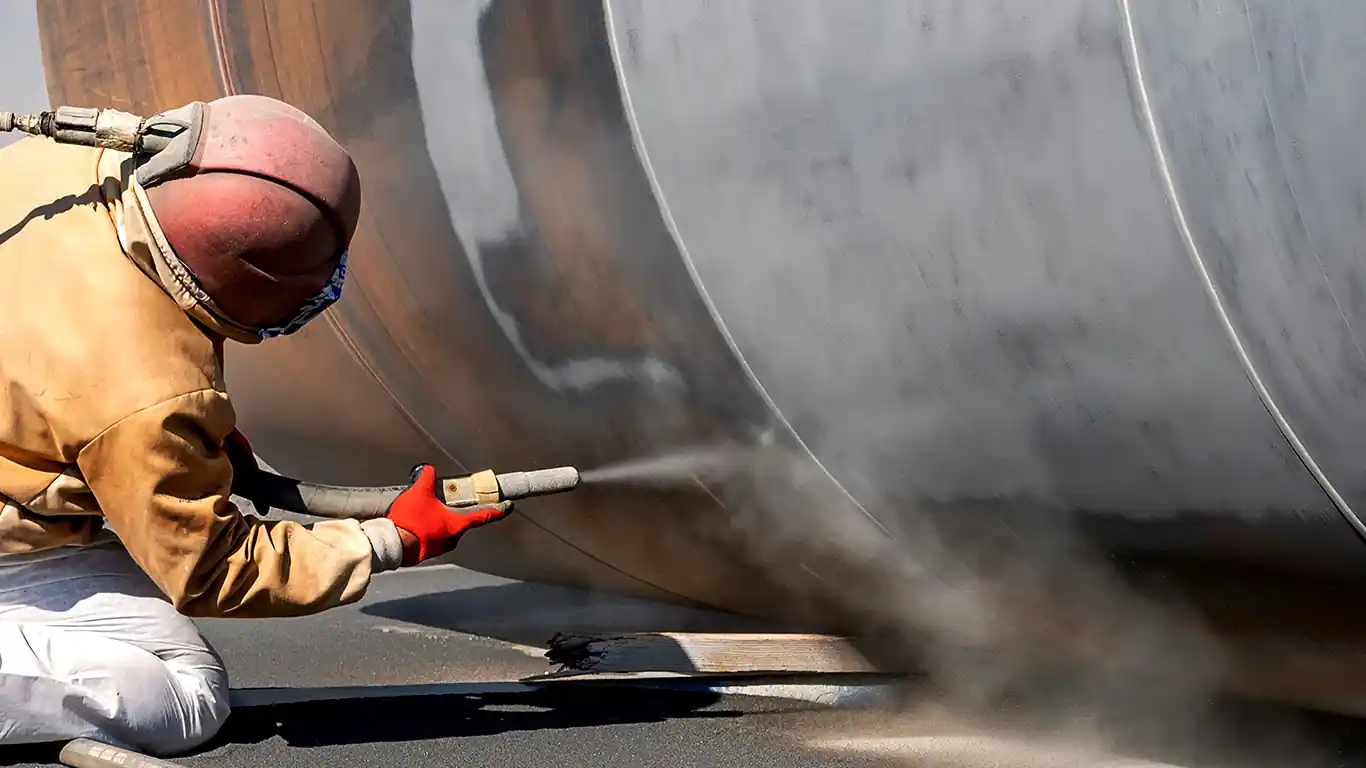
Today, sandblasters are using a variety of abrasive media including steel grit for metal surfaces, plastic particles and walnut shells for wood, garnet or crushed glass for concrete. Other variations include aluminum oxide, copper slag, silicon carbide, and silica-free sand. Some of these media break up into dust particles that still carry harmful substances.
OSHA requires employers to detail an Exposure Control Plan, provide protective clothing and respirators, close off sandblasting inside a ventilated area and provide employees exposed to blasting with medical examination and periodic testing. Rather than dry sweeping and using compressed air to clean employee clothing, they’d use vacuuming or wet sweeping and install cleanroom air showers to remove dust.
At this point, it may be necessary to reevaluate the perceived “inexpensive” factor of sandblasting. In part, it was the significant financial burden imposed on businesses that delayed the enactment of the modern silica exposure limit. A 2013 estimate by OSHA was $657 million each year.
Yet that’s not all. In addition to the health risks for workers and the costs associated with extra safety measures, blast cleaning relies on a continuous supply of raw materials and accumulates secondary waste in instances when the abrasive media cannot be reused or recycled. While properly disposing of organic material like walnut shells seems like a doable task, other abrasive media used in industrial settings, combined with the contaminants removed from a surface, increase the company’s environmental footprint.
It’s about time a better solution emerged.
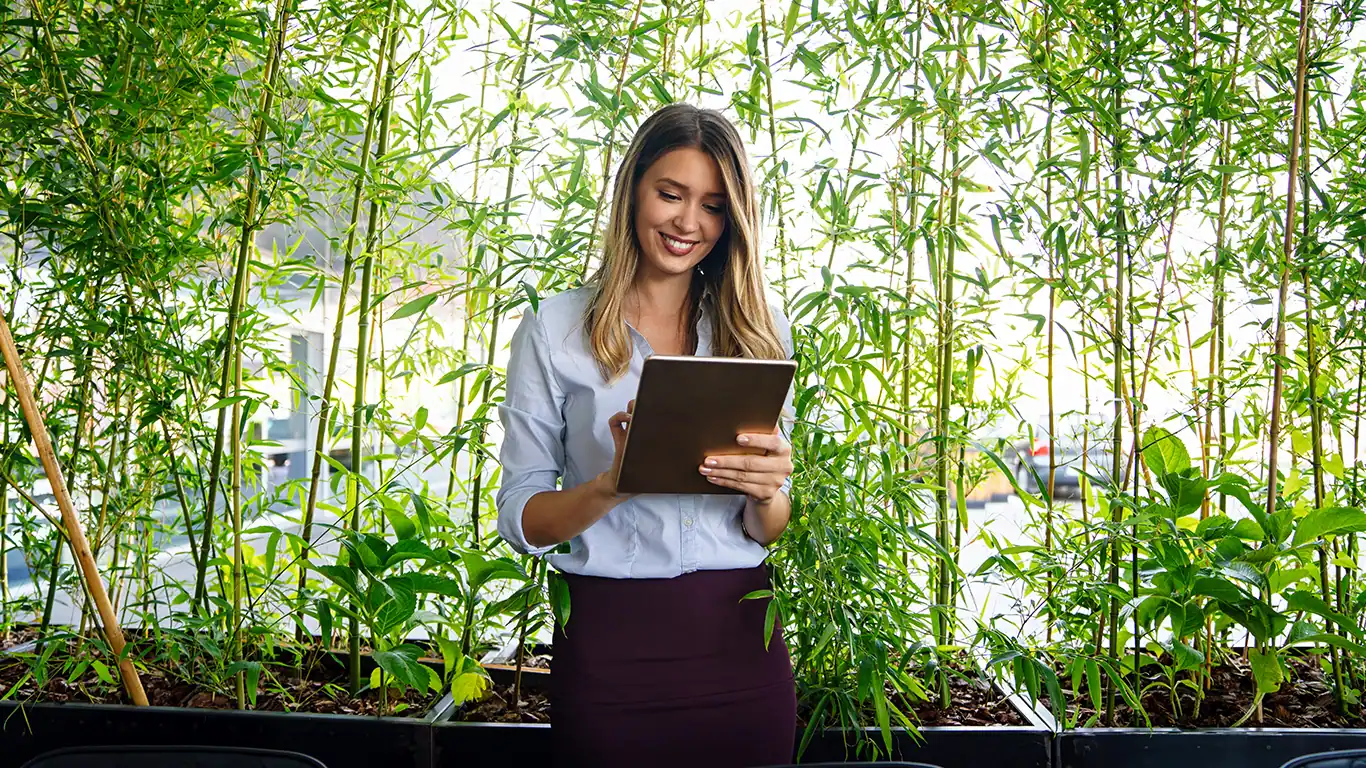
More Benefits, Less Hassle
Fiber laser technology comes in diverse configurations, available in both open and enclosed systems. In cleaning applications, the power output ranges from 50 watts to several kilowatts. The systems are designed with either pulsed or continuous wave (CW) laser technology to suit operations that vary in scale and complexity. Within a system, the output power, as well as the lasing pattern and duration, are adjustable. Laser systems are also easily automated and integrated into production lines.
As an alternative to sandblasting, laser tools offer precision that blast cleaning often cannot match. A contactless procedure, laser processing minimizes the margin of error and only alters the micro-surface of the material. And here’s where the sustainability factor comes in: laser cleaning requires no abrasive media or chemicals, significantly reducing handling costs and industrial waste.
As with any machinery, however, there are risks that everyone must take into consideration before operating a laser system. Laser ablation involves high-energy light beam emission that can become a fire hazard. The regulation of laser technology in the United States is primarily overseen by the FDA’s Center for Devices and Radiological Health (CDRH). Rules include proper labelling of the hazard classes and adhering to safety measures that minimize the risk of radiation exposure to skin and eyes.
The flagship CleanTech products by Laser Photonics come under the CDRH Class I and Class IV rating. We equip our laser cleaning systems with safety interlocks, emission indicators, emergency stop, overheat protection, and air pressure sensors. Laser Photonics also provides professional training to operators of the machinery in the United States and abroad.
Laser Photonics a Laser Cleaning Powerhouse
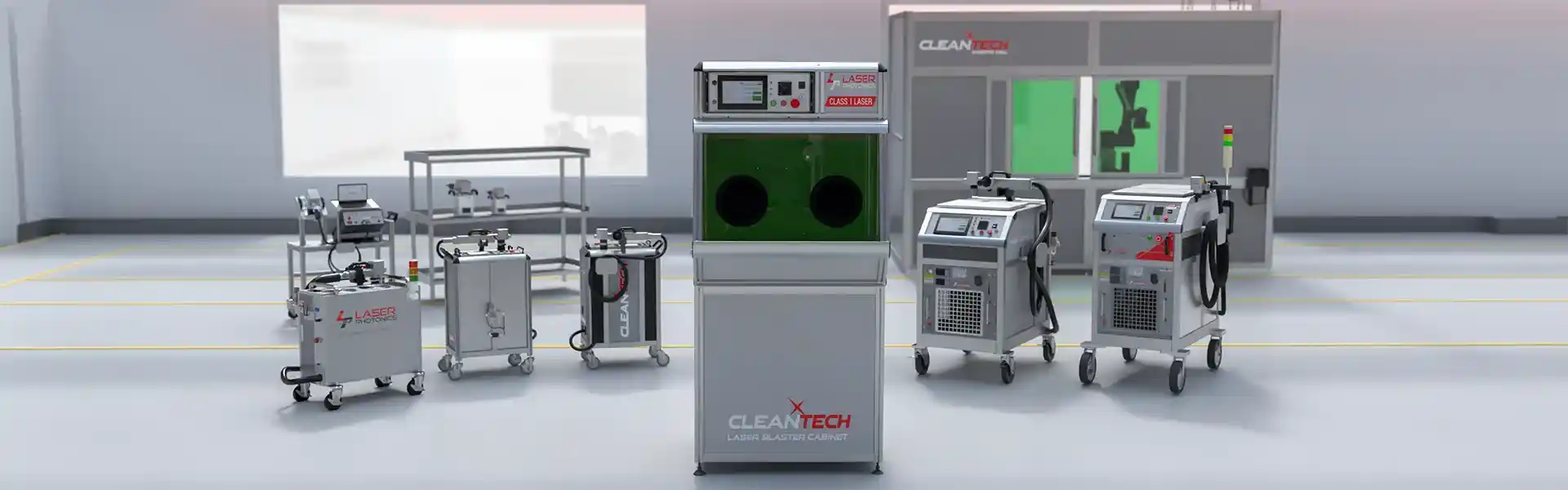
Laser Photonics was one of the first to build a laser cleaning system that integrated CW laser technology, which improved throughput without compromising affordability. A powerful CW laser can also be used for texturing and is often used for priming to improve resistance and adhesion. At the low-power end of the spectrum, pulsed lasers are more efficient and can be used to melt the micro-surface for a polished finish.
That is how Laser Photonics categorizes its laser cleaning products, designating them into finishing, conditioning, or roughening material processing classes. Our latest, next-generation, products in the pipeline feature smaller-than-ever handheld scanheads, mobile connectivity, and a compact overall design. These transportable systems come in handy for tasks that require frequent operator mobility.
On the other hand, we design enclosed Class I standalone laser systems. These are customized and can integrate a rotary indexer for circumferential processing; a fume extractor for applications requiring the vaporization of toxic substances; a robotic arm for automated operations; and mechanisms for shuttling workpieces through the system.
Plus, we are always on standby to take on custom engineering requests.
Long-Term Value Outweighs Initial Affordability
The choice between laser cleaning vs sandblasting ultimately hinges on the accessibility of the equipment, its capabilities, and your initial investment capital. Today, blast cleaning remains the common cleaning method as the equipment is more widely available. Individual consumers can easily purchase sandblasting products from major retailers, while laser cleaning systems are targeted almost exclusively at businesses and may not be instantly available as an emerging technology. However, as alarms sound against the environmental and health implications associated with the dust and debris that bast cleaning generates, professionals are seeking better options.
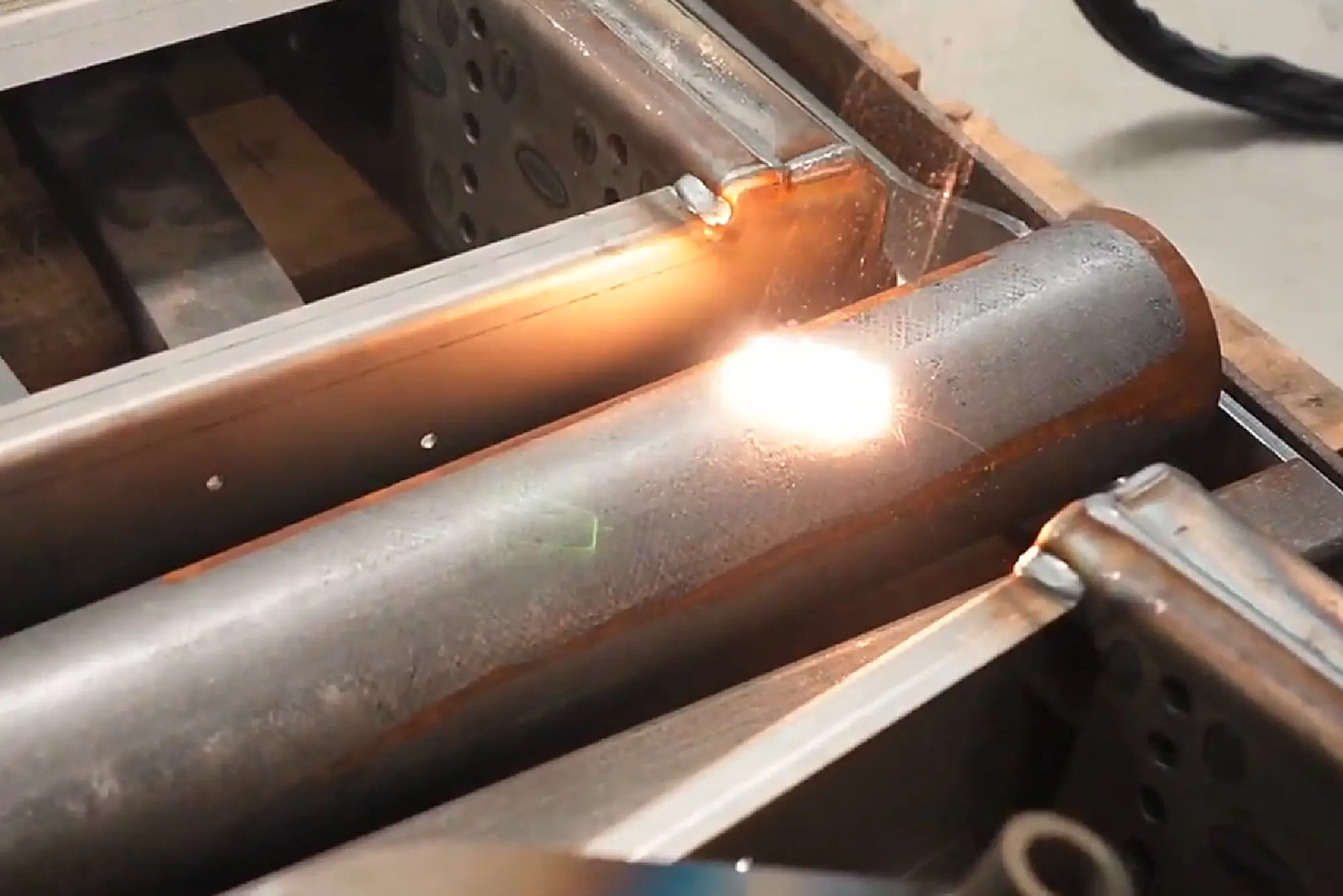
At Laser Photonics, we are committed to delivering innovative solutions to those in need. Laser cleaning stands out for its precision and eco-friendliness, providing a safe, non-contact surface processing method. While it may come with a higher initial investment, the long-term benefits of the reduced costs of cleanup, maintenance, and well-being protection cannot be overlooked.
As we move toward a more environmentally conscious and health-centric industrial landscape, the world continues to adopt laser cleaning technology as an alternative to sandblasting. Innovations in laser systems are making them more accessible and broadening their capabilities for various applications and industries.
Regardless of the cleaning method chosen, it is imperative for operators to adhere to safety standards and regulations to ensure a safe working environment. By weighing the pros and cons of each method, businesses can make informed decisions that align with their operational goals and commitment to sustainability.
Speak to a Laser Specialist