How Laser Technology Modernizes Product Traceability
Tracing a product through its entire life cycle – from procurement through assembly, utilization, repair, and recycling – allows manufacturers to differentiate in a competitive market, identify and mitigate issues, comply with regulations, and maximize efficiency. Yet while advanced data management has become integral to smart manufacturing, standard product identification processes have fallen short.
The pressing demand for modern identification methods for product traceability has driven the adoption of laser marking technology. Today, laser marking tools are implemented by industries across the board. These are high-speed, consumable-less systems with variable power lasers that can mark materials on the fly – permanently.
So, how does laser marking compare to other methods? In this broad overview, we’ll zoom in on a few common marking techniques and highlight their pros and cons in comparison to laser marking. We’ll cover how laser marking is used and explore what makes this technology stand out in the modern industrial landscape.
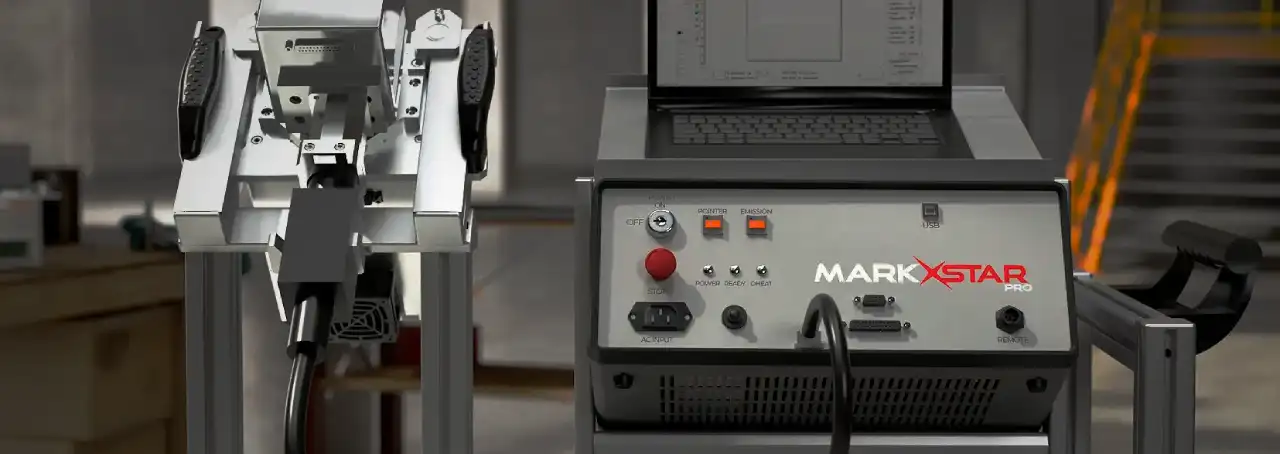
Impact, Ink & Electrolytic Marking
Common marking techniques rely on either mechanical impact, ink stamping, or a combination of electricity and electrolytes.
Impact Marking
Impact marking, typical for industrial settings, works by creating physical impressions or milling into targeted material. In the first scenario, a dot peen machine rapidly strikes a surface with a carbide pin, creating a series of dots that together form a recognizable pattern. In the second case, a CNC mill grinds into the surface with a rotating cutting bit to remove a layer of material and leave an indented design.
The pros of impact marking technology include the durability of the marks, its ability to be easily integrated into production lines, and its relative affordability, which is dependent on the design of the system. The cons are its limited depth of marking, a regular need for dot pin or bit replacements, and machine maintenance. In addition to this information, the precision in mechanical marking methods like dot peening and CNC milling is constrained by the physical size of the tools. This renders the method unsuitable for applications like micromarking.
Ink Marking
Another distinct approach to marking is ink printing or stamping. During this process, inks are applied directly onto a wide range of materials via mesh screens and layered stencils. The main advantage of this approach is the coloration that other marking methods do not offer. It is also versatile, suitable for materials from rigid to heat-sensitive. However, screen printing may be time-consuming and comes with substantial costs for consumable materials and labor. Moreover, and most critically, the design it produces can fade over time or be removed by abrasion.
Inkjet marking is a similar but simpler and faster process that works much like an office printer. This approach involves spraying ink onto a surface to create markings and shares similar drawbacks to screen printing, like lack of durability and a need for ink refills.
Electrochemical Marking
Lastly, electrochemical marking is a simple technique that involves an electrical current, an electrolyte fluid, and a neutralizing fluid. The first two are used to oxidize a metal and create a permanent, discolored imprint, while the neutralizer restores its pH neutrality. The downsides to this fast and economic method are that electrochemical marking is limited to conductive metal surfaces and requires proper stencils, chemicals, and applicators. It may be quite challenging to apply electrochemical marking in confined areas and in high-volume production.
Let’s now delve into the processes behind innovative laser marking technology.
Laser Marking, Explained
A laser marking system uses the heat generated by a laser beam to either ablate or anneal the target surface in a programmed pattern. During ablation, laser pulses break down molecules of the surface, vaporizing them and leaving an indented design. During annealing, the laser’s heat modifies the microstructure of the surface, changing its visual appearance by discoloration. This marking is permanent and highly precise.
A laser engraving system works the same way but has built-in Z-axis movement capability. Simply put, the focus of an engraving laser can move vertically up and down to ablate material lower than the surface level and create a 3D indentation. Z-axis positioning can be either mechanical or automated, depending on the system build.
Graphics for laser marking are typically programmed using CAD software. For portable systems, graphics can be designed on a PC and then transferred to the laser marker. Laser marking systems are flexible on input and allow easy automation and integration into production processes.
Types of Lasers & Their Applications
Standard laser marking technology integrates a laser operating in either fiber, CO2, or UV wavelength.
A fiber laser marking machine – which generates an infrared laser beam inside an optical fiber – effectively marks stainless steel, aluminum, alloys, thermoplastics, silicon, and more. Enterprises across the automotive, aerospace, defense, maritime, energy, and semiconductor sectors, to name a few, adopt this technology for high-volume, heavy-duty use.
Another type of laser marker, a CO2 laser marking machine, generates laser light inside a tube with a mixture of CO2 and other gases. This technology is typically used in marking softer materials like wood, ceramics, glass, and fabric. Between the two technologies, fiber laser marking is faster and more energy efficient. Meanwhile, a CO2 laser marking system generally comes with a smaller price tag, which makes this solution popular in artisanal and small-business applications.
Lastly, an ultraviolet (UV) laser marking machine – less common and more costly – would excel in ultra-precision applications where the material is sensitive to heat. A UV laser emits light in short wavelengths, which certain materials absorb more readily than infrared light. This technology is used in fields like medical device manufacturing and micromachining, where fine precision is crucial.
Laser Marking in Comparison
Laser marking has some great advantages over other methods of industrial marking.
When it comes to precision, laser marking has no equal. The laser light is highly concentrated and focused into an incredibly small beam which scans the surface in a desired pattern. This allows laser marking technology to create intricate and complex designs that are difficult to achieve with mechanical tools. Thanks to this small beam, a laser can effectively mark in narrow crevices and hard-to-reach areas. In addition, as a contactless processing method, laser marking poses no impact stress on the workpiece, which makes it suitable for thin and delicate materials.
Laser marking has some great advantages over other methods of industrial marking.
When it comes to precision, laser marking has no equal. The laser light is highly concentrated and focused into an incredibly small beam which scans the surface in a desired pattern. This allows laser marking technology to create intricate and complex designs that are difficult to achieve with mechanical tools. Thanks to this small beam, a laser can effectively mark in narrow crevices and hard-to-reach areas. In addition, as a contactless processing method, laser marking poses no impact stress on the workpiece, which makes it suitable for thin and delicate materials.
Industrial laser marking is also a winner in durability. While impact and electrochemical marking provide similar permanence, ink printing is often perishable and unsuitable for applications such as product traceability and regulatory compliance.
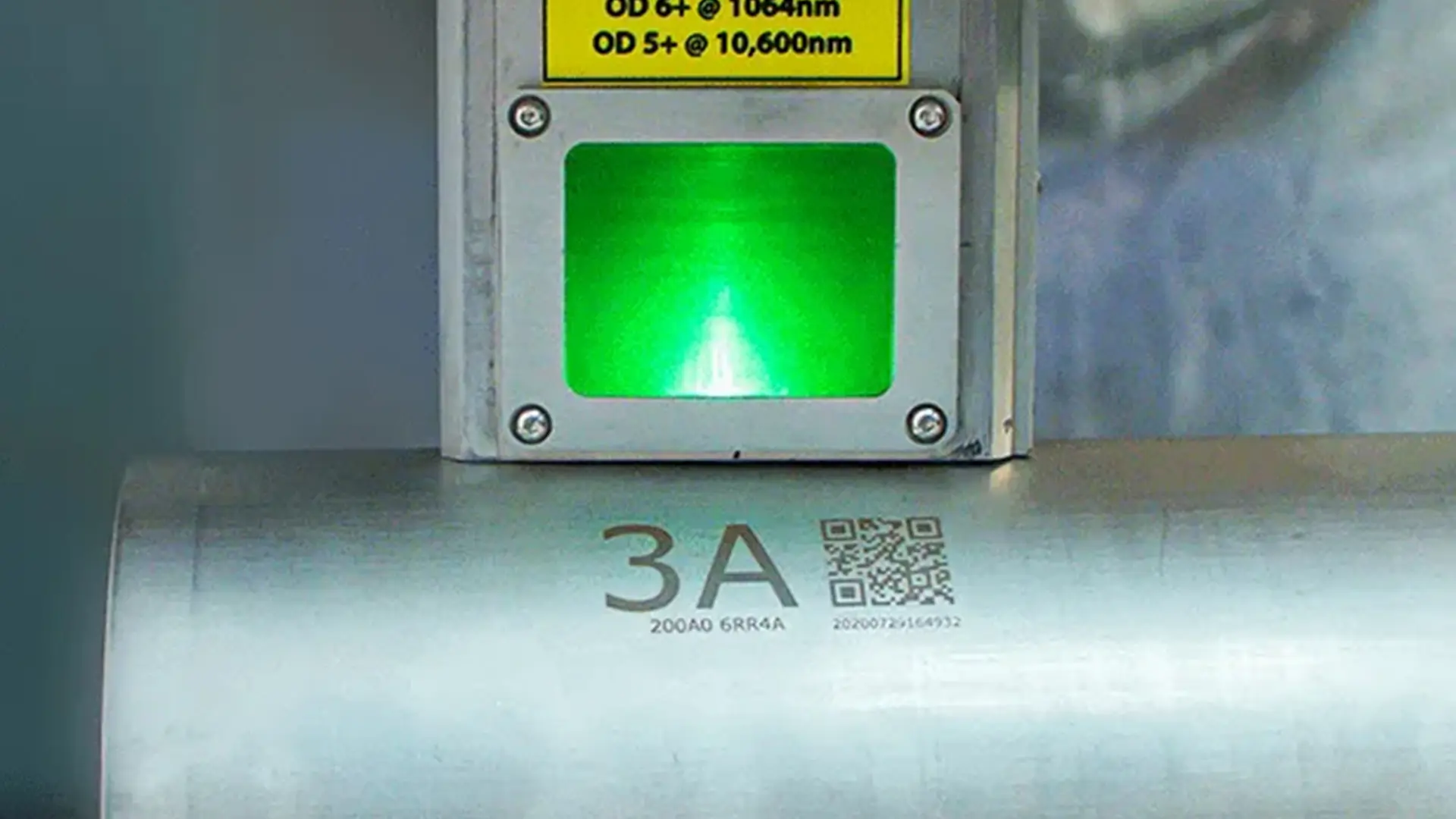
In terms of versatility, laser marking tools also carry an advantage. The laser’s parameters, including power, focus, pulse duration, and oscillation can be fine-tuned to suit specific materials and applications. Additionally, unlike other methods, laser marking and engraving offers depth variability. Yet laser marking best suits materials with some degree of heat resistance. Short-pulse laser processing generates a minimal heat-affected zone and results in minimal, if any, warping of the base material.
Taking into consideration the costs of comparable methods, industrial laser marking typically involves a higher initial investment, depending on the system configuration. Yet in the long term, this price leads to greater returns than marking methods that require regular maintenance and replenishment of materials. A laser marking system offers lasting performance with consistent use and requires no consumables or frequent maintenance.
Lastly, laser marking is a sound choice for sustainability-oriented businesses. The ecological footprint of traditional marking solutions remains unresolved, as the ongoing need for mill bits, ink, chemicals, and other consumables continues to accumulate waste. Professionals switching to laser processing technology cut back consumption and waste in their operations.
Choosing the Right Marking Tool for Your Needs
You may be seeking a new product identification solution to modernize traceability, branding, quality control, and inventory management. When considering an upgrade for the marking processes in your business, many factors come into play.
If product traceability isn’t optional in your field, you’re likely looking for tamper-proof marking technology. The right marking tool for your business should also be effective in terms of throughput, usability, precision, resources, safety, and sustainability. And if you have gotten this far in exploring the advantages of laser marking over the pros and cons of other techniques, you might be ready for the next step – choosing the right laser marking tool.
Your laser marking machine of choice will be directed by the materials to mark and their sensitivity to heat. As previously mentioned, there are several types of lasers – fiber, CO2, and UV – each better suited for specific materials and the level of detail required.
Consider also the maneuverability of your laser marking system or its integration into existing production lines. Do your operations require handheld positioning or automated marking? Are you looking for deep engraving capability or marking in hard-to-reach areas? Will you need a rotary indexer for circumferential marking? What level of detail are you looking to achieve?
Laser specialists at Laser Photonics can help you choose the laser marking solution that best suits your operations. In our portfolio of laser processing systems, you will find marking solutions in a variety of configurations, from a portable, handheld laser marking machine to a stationery, enclosed engraving system with automated shuttling of parts. And if you’ve got something in mind that you don’t immediately see among our products, contact us – our engineers are on standby to offer custom-tailored options.