Unlike other forms of thermal electricity generation, all waste from nuclear power plants is regulated and contained. Radwaste management is critical due to a complex interplay of environmental, safety, economic, and logistical challenges associated with radioactive materials and the increasing volume of nuclear decommissioning activities. Yet common cleaning methods at nuclear reactors are often inefficient due to significant drawbacks, primarily involving the spread of contamination.
Laser Photonics offers a different solution – advanced laser technology with demonstrated effectiveness in removing contamination from solid surfaces.
Main Risk in Nuclear Power Generation
The use of nuclear power as a source of energy continues to raise debate today. A very small amount of nuclear fuel produces a very large amount of energy – plus a small amount of waste. But this waste is radioactive.
Indeed, unlike coal-burning power plants, nuclear fission does not produce soot and carbon dioxide – but the mining, processing, and use of nuclear fuel generate radioactive wastes that are difficult to handle. Radioactive particles accumulate on components and infrastructure over long-term service as loose contaminated layers and fixed oxide layers on surfaces.
Exposure to radwaste carries significant risks. Radioactive elements can penetrate and damage living matter, potentially causing damage to human health and long-term harm to the environment. This waste must be securely stored in specialized facilities over decades or even centuries for radioactive decay.
Ongoing concerns center on the risk of radwaste leakage – should containment fail, the resulting spillage could pose serious environmental and public health hazards.
Maintenance of nuclear power plants in operation and the decommissioning of assets 30-40 years later for safety purposes necessitate adequate radwaste management measures. As of 2023, 22 commercial nuclear reactors were in various stages of decommissioning in the United States. Among 94 reactors that are now active, more than half will see their licenses expire over the next two decades.
Despite ongoing efforts, universally acceptable solutions for cleaning, recycling, and disposing of contaminated assets and waste remain elusive.
Laser Decontamination an Effective Solution
What laser cleaning offers is a promising method for recovering costly equipment and mitigating risks associated with radwaste. A laser is capable of completely removing top layers from solid surfaces like metal and concrete. These layers can be comprised of oxides, anti-rust coatings, paint and epoxy, silicates, anodization, or other deposits. Powerful fiber laser systems have demonstrated effectiveness in the near-100% removal of alpha contamination and a significant reduction in beta particle concentration in one pass, with complete decontamination after a second pass.
This process is highly controllable due to the varying ablation thresholds – the specific energy levels at which the receiving material disintegrates at the particle level. By properly setting the irradiation parameters including power density, pulse frequency and duration, and positioning the beam at the focal distance from the surface, the top layer can be precisely removed without damage to the base material.
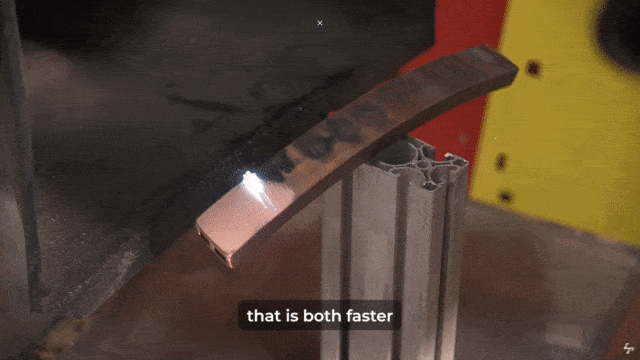
Fume Extraction & Filters
Laser processing in nuclear power applications must be paired with a fume extraction system equipped with multi-stage filters, often in conjunction with sealed environments. While laser cleaning generates minimal secondary waste compared to cleaning by water jet or abrasive grit blasting, it gasifies contaminants, producing airborne particles that must be contained. During ablation, a strong point-source vacuum system immediately captures these gasified residues, which are then trapped by HEPA or other high-efficiency filters. These filters become radioactive waste and are treated accordingly.
Visionaries Like IUPAT Adopt Laser Cleaning
Today, laser cleaning is increasingly used at nuclear power plants. In this video, you can find out how Bruce Power implements laser systems to quickly remove paint, rust, and coatings at its nuclear facilities in Ontario, Canada. The International Union of Painters and Allied Trades (IUPAT), whose members participated in the referenced video, is among the proactive adopters of laser cleaning technology. Servicing the United States and Canada, IUPAT employs CleanTech tools not only at nuclear power plants, but across other power generating centers and job sites.
Laser Photonics asked Jerett Patey, Business Representative at IUPAT, about the trade union’s choice of decontamination equipment and its experience with laser ablation tools. Patey said:
“When it comes to removing coatings with sandblasting, it requires a lot of energy, heavy equipment, and generates a significant amount of waste. In contrast, using a laser system with a fume extractor drastically reduces waste. We’re talking about producing just a few pounds of waste instead of tons. And if that waste is hazardous – like radwaste or lead paint – it becomes contaminated and costly to handle and dispose of. With the laser process, you’re essentially just dealing with the filter from the fume extractor, which is far simpler and more cost-effective.”
According to Patey, the IUPAT “thrives on safety,” boasting a safety rate that is 33% higher than non-union contractors. The union ensures its workers undergo extensive training before arriving onsite and works closely with technology manufacturers to gain a deep understanding of the systems.
Laser Photonics’ Genti Zeqo with Jerett Patey and Nelson Garbett from the International Union of Painters and Allied Trades (IUPAT)
As part of its adoption of CleanTech laser decontamination tools, IUPAT collaborated with Laser Photonics in testing the technology at its training facility in Ontario. According to Patey, the results were highly encouraging, and IUPAT’s members are now using CleanTech at multiple sites. He said:
“Laser ablation, combined with a fume extractor, allows us to complete the work more quickly and with fewer scheduling disruptions. Unlike old methods that require shutting down, de-energizing, or isolating equipment, the laser system can often be used without those steps – delivering the same results with far less impact on operations.
We’re currently working with three nuclear power plants, using the CleanTech equipment as needed – especially in vaults and contaminated areas. The goal is to get our members in, complete the work efficiently, and get them out quickly. The old way – stripping paint, sandblasting, repainting, and then cleaning up – meant longer exposure times for workers. By reducing that exposure, we’re not only protecting our members but also improving efficiency. For plant operators, this means less downtime and lower costs. And for us, it means safer conditions for our members. Scheduling and outages are critical to a power plant’s success – so if we can save time and do it more safely, why wouldn’t we?”
Patey concluded that laser technology is going to make work significantly safer, easier, and faster. For the nuclear power plant, the advantages are reducing downtime, streamlining scheduling, and minimizing waste – which can lead to substantial cost savings. He added: “We’re proud to be part of that solution.”
Laser Use in Line With Nuclear Energy Incentive
The national energy policy is shifting toward revitalizing nuclear power – with ambitious goals like quadrupling domestic capacity to 400 GW by 2050 to fulfill the growing need for energy independence. Thus, the need for safer, more efficient maintenance and radwaste management solutions is becoming urgent for a growing fleet of nuclear facilities. Laser cleaning technology aligns perfectly with these priorities. By enabling precise, non-contact decontamination with minimal secondary waste, it supports both routine maintenance and the complex demands of decommissioning.
The example set by IUPAT and facilities like Bruce Power demonstrates that laser ablation is no longer theoretical. It is a proven, field-tested solution already driving measurable gains in safety, scheduling, and cost reduction. As the nuclear sector expands under supportive policy frameworks, technologies like CleanTech offer a pathway to modernize operations, recover valuable assets, and minimize downtime – all while enhancing worker safety and environmental stewardship.
Laser Photonics supports the nuclear industry by delivering advanced laser cleaning solutions that help extend reactor lifespans, increase capacity, and modernize infrastructure – ultimately contributing to a cleaner, more efficient future for nuclear energy.
Speak to a Laser Specialist